Unternehmensgeschichte
- Details
- Kategorie: Unternehmen
Tradition trifft auf Innovation – Unternehmen, die auf eine lange und bewegte Geschichte zurückblicken, müssen irgendwo ihren Anfang genommen haben.
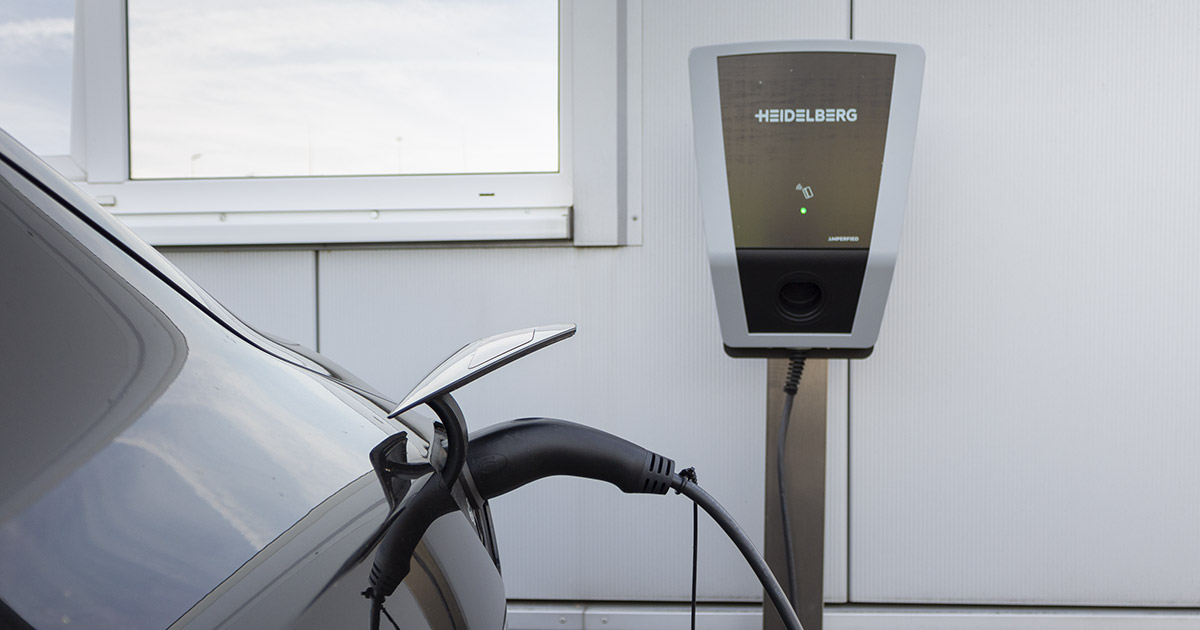
2024
- Details
- Kategorie: Unternehmensgeschichte
Mit dem HP Latex 1500 hält ein Rollendrucker mit 3,20 Meter Breite Einzug in den Großformatdruck. Die wasserbasierten Latex-Farben ermöglichen eine ausgezeichnete Farbwiedergabe für Printprodukte im Indoor- wie im Outdoor-Einsatz.
2023
- Details
- Kategorie: Unternehmensgeschichte
In Rostock wird ein Kern Außenbüro eingerichtet, das mit zwei Grafikerinnen die Mediengestaltung in Bexbach personell verstärkt. Mit dem Weggang der beiden muss das Büro allerdings schon nach einem Jahr wieder geschlossen werden.
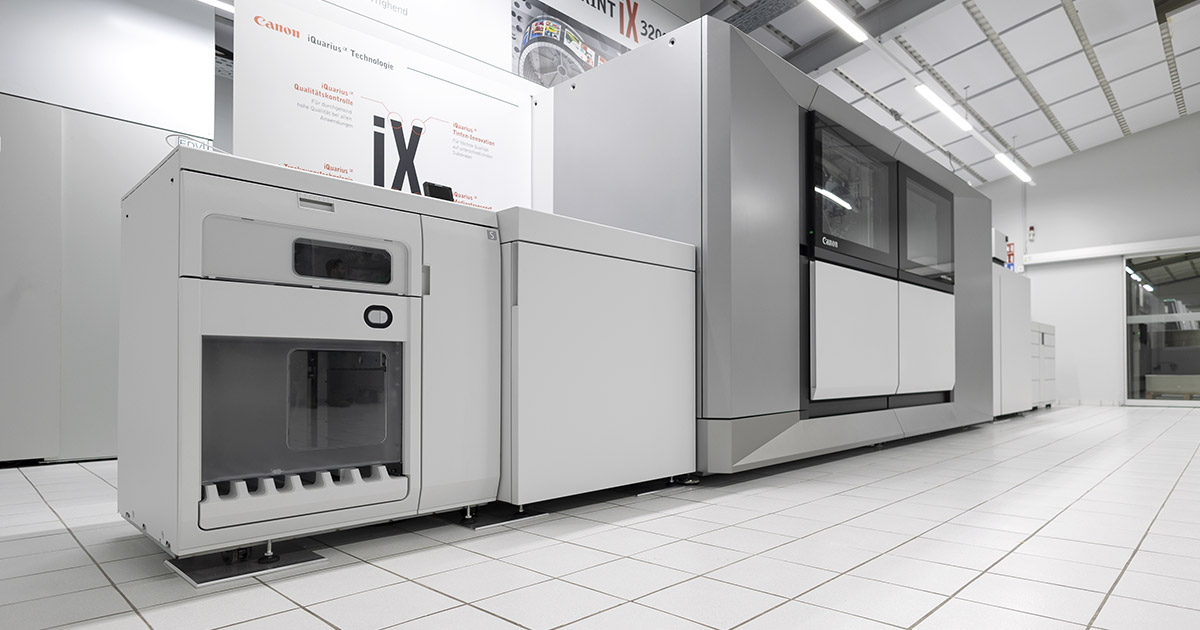
2022
- Details
- Kategorie: Unternehmensgeschichte
Mit der Canon varioPRINT iX3200 wird der bisher tonerbasierte Farbdigitaldruck auf der Kodak NexPress SX3300 durch ein Hochleistungstintenstrahlsystem ersetzt. Der Großformatdruck wird durch einen zweiten Epson SureColor SC-S80600 Solventrollendrucker verstärkt.
2021
- Details
- Kategorie: Unternehmensgeschichte
Als Folge der Corona-Pandemie und dem geringen Druckaufkommen wird eine Lücke in den Recycling-Kreislauf von Altpapier gerissen. Die sich durch verändertes Konsumverhalten und die Umstellung der Papierindustrie von grafischen Papieren auf die Herstellung von Verpackungsmitteln bereits abzeichnende Papierkrise schlägt voll ein. Die Verfügbarkeit auf dem Papiermarkt bricht ein, Lieferzeiten erhöhen sich von wenigen Tagen auf teils mehrere Monate. Kern kann die Durststrecke durch das große Papierlager in Halle 2 und zusätzlich temporäre Lagerflächen erfolgreich überbrücken und einen großen Teil der Papiersorten vorrätig halten.
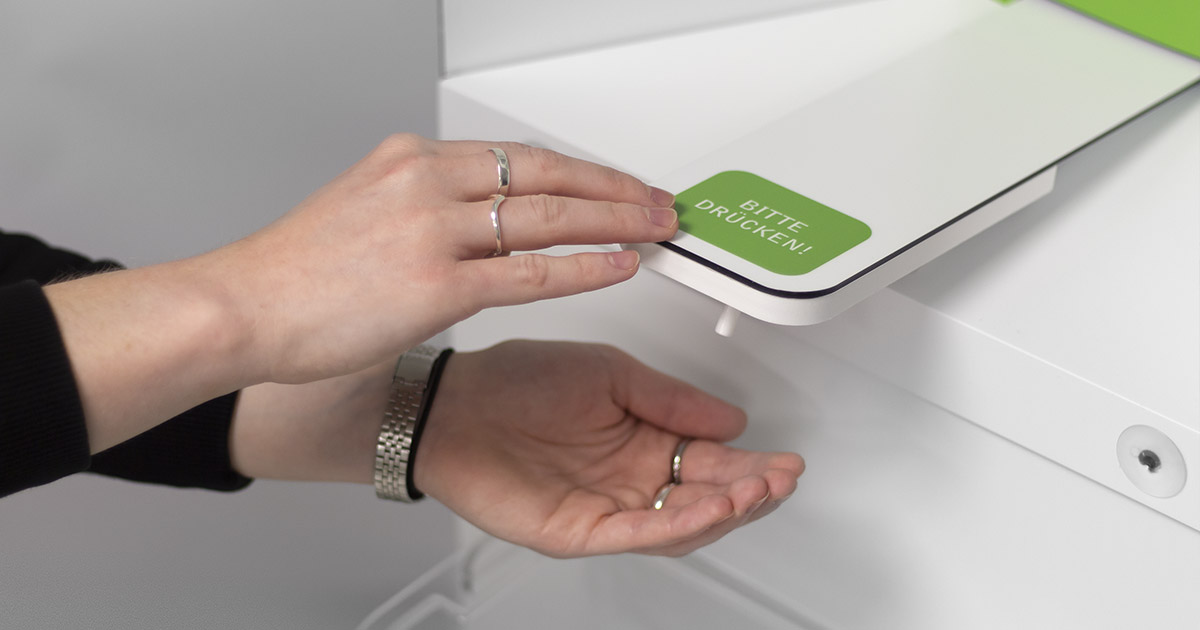
2020
- Details
- Kategorie: Unternehmensgeschichte
Die Corona-Pandemie trifft alle Branchen hart. Geschäfte bleiben geschlossen, Messen werden abgesagt, Kultur- und Sportveranstaltungen finden nicht mehr statt – der Druckmarkt bricht ein. Die frei werdenden Kräfte aus Offsetdruck, Digitaldruck und Druckverarbeitung werden im Großformatdruck gebündelt, wo am laufenden Band Desinfektionssäulen hergestellt werden. Neben zugekauften Spendern für die individuell bedruckten Displays aus Aluverbundmaterial wird ein eigenes Spendersystem entwickelt, mit dem Kern bei den Druck & Medien Awards zum LFP-Drucker des Jahres gekürt wird.
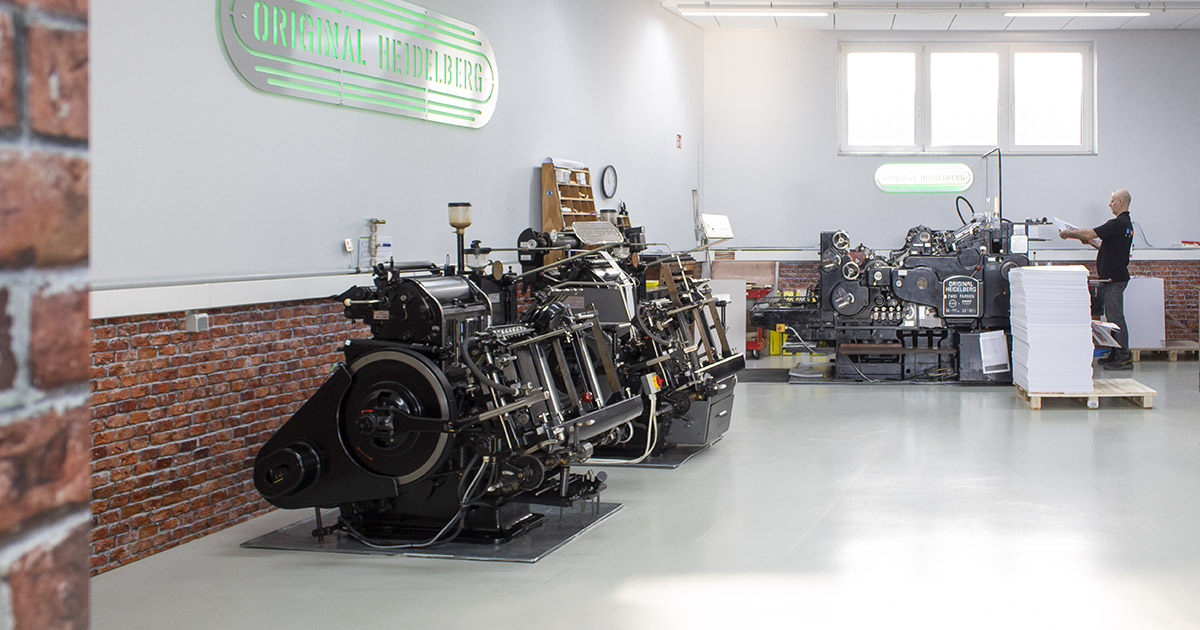
2019
- Details
- Kategorie: Unternehmensgeschichte
Die Letterpress-Abteilung wird vom Offsetdrucksaal in einen eigenen Bereich für Druckveredelung in Halle 1 ausgelagert. Der Original Heidelberger Tiegel (OHT) wird um einen zweiten für Heißfolienprägung ergänzt. Auf einer Original Heidelberger Zylinderpresse (OHZ) werden Weiterverarbeitungsschritte wie Stanzen, Rillen und Perforieren vollzogen. Auch die Zellophanierung zieht vom Digitaldruck in den Bereich um.
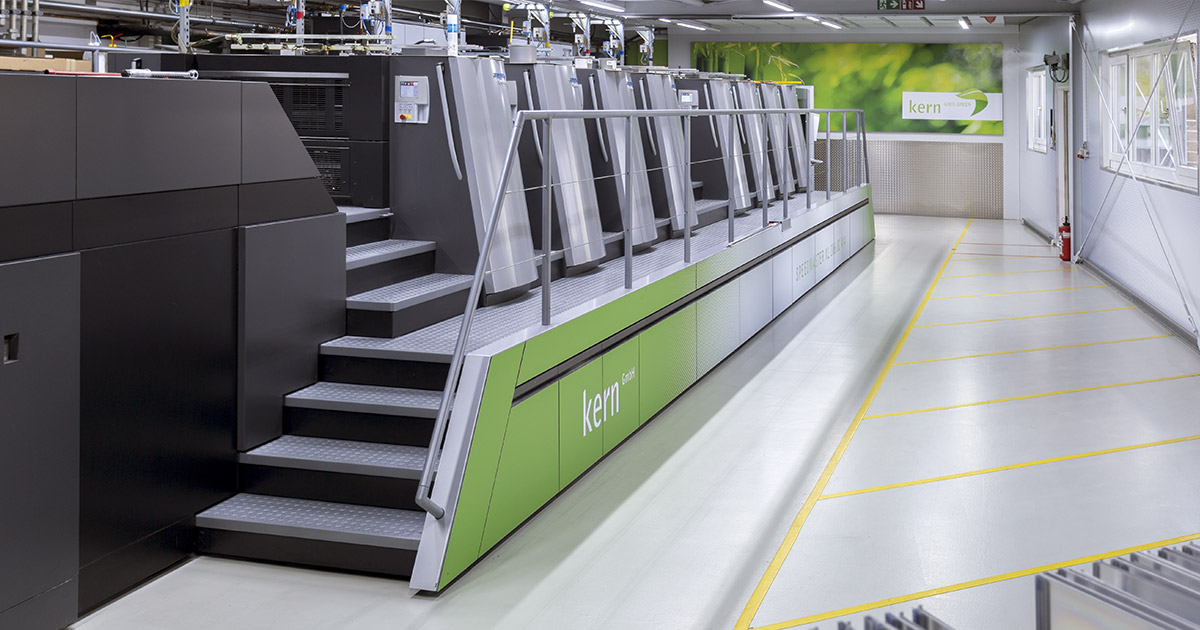
2018
- Details
- Kategorie: Unternehmensgeschichte
Mit dem Austausch der Achtfarbenoffsetmaschine im Januar – ebenfalls durch eine Maschine der XL-106-Reihe – ist der Erneuerungszyklus im Drucksaal abgeschlossen. Die beiden neuen Speedmaster XL ergänzen sich dabei optimal – der Auflagendruck der Broschüren erfolgt auf der Achtfarbenmaschine mit vollautomatischer Bogenwendung, auf der Fünffarbenmaschine werden Umschläge mit Sonderfarben, UV-Lackverdelung und Inline-Verarbeitung wie Perforieren, Stanzen oder Rillen hergestellt. Damit erreicht der Druckprozess eine Peak Performance, die besonders im Bereich der Katalog- und Magazinproduktion zum Tragen kommt.
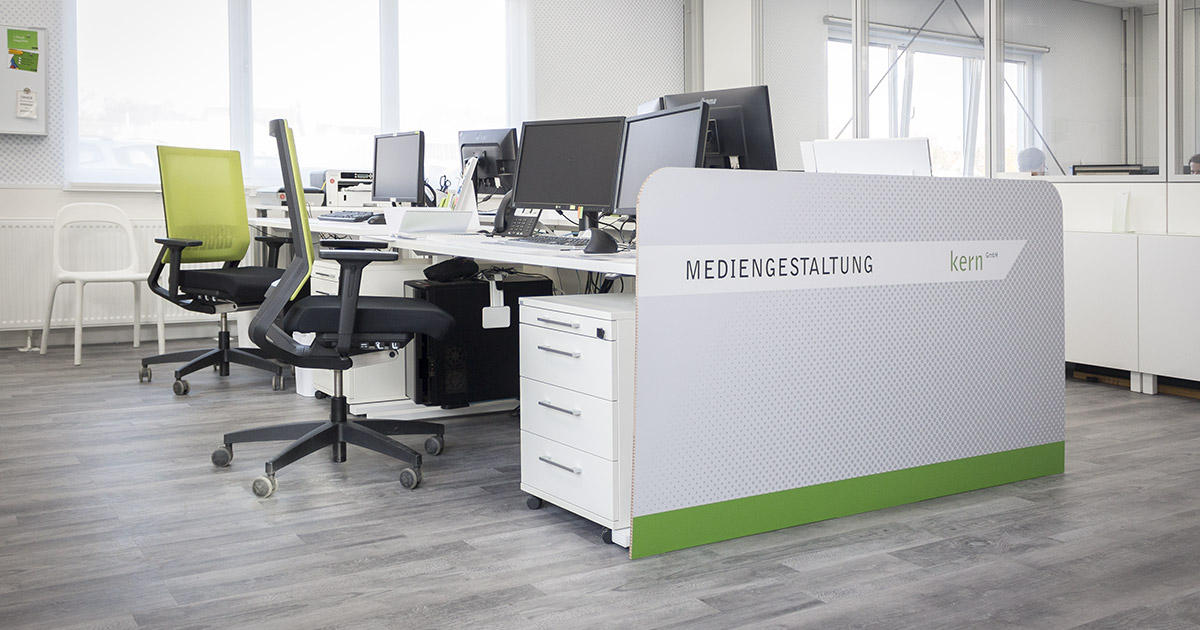
2017
- Details
- Kategorie: Unternehmensgeschichte
Den nächsten Schritt im Erneuerungszyklus bildet im März der Austausch der Heidelberg Speedmaster CX 102 durch eine XL 106 5+L (UV-Lack). Neben dem höheren Durchsatz von bis zu 18.000 Bogen pro Stunde und einem größeren Papierformat, das mehr Möglichkeiten zur effektiven Ausnutzung des Formats mit Sammelformen bietet, können mit der XL 106 erstmals im Haus UV-Lack-Veredelungen ausgeführt werden. Mittels Push-to-Stop-Prinzip und vollautomatischem Plattenwechsel werden Auftragswechsel in gerade einmal drei Minuten vollzogen. Einrichteprozesse müssen nicht mehr erst aktiv vom Bediener gestartet werden, sondern werden von der Druckmaschine autonom initiiert.
2016
- Details
- Kategorie: Unternehmensgeschichte
Im Sommer wird der gesamte technische Ablauf im Offsetdruck-Workflow umstrukturiert. Die bestehende Heidelberg Prinect Umgebung wurde auf die aktuellste Version gebracht und um das Management-Informationssystem (MIS) Businessmanager erweitert. Hierfür waren umfangreiche Serverumrüstungen erforderlich.
2015
- Details
- Kategorie: Unternehmensgeschichte
Mit der neuen Halle 2 wird im Herbst der Großformatdruck ausgebaut. Der Durst Rho P10-160 UV-Drucker kann Plattenmaterial wie Karton, Holz, Kunststoff, Metall oder Plexiglas bis zu einer Stärke von 40 mm direkt bedrucken.
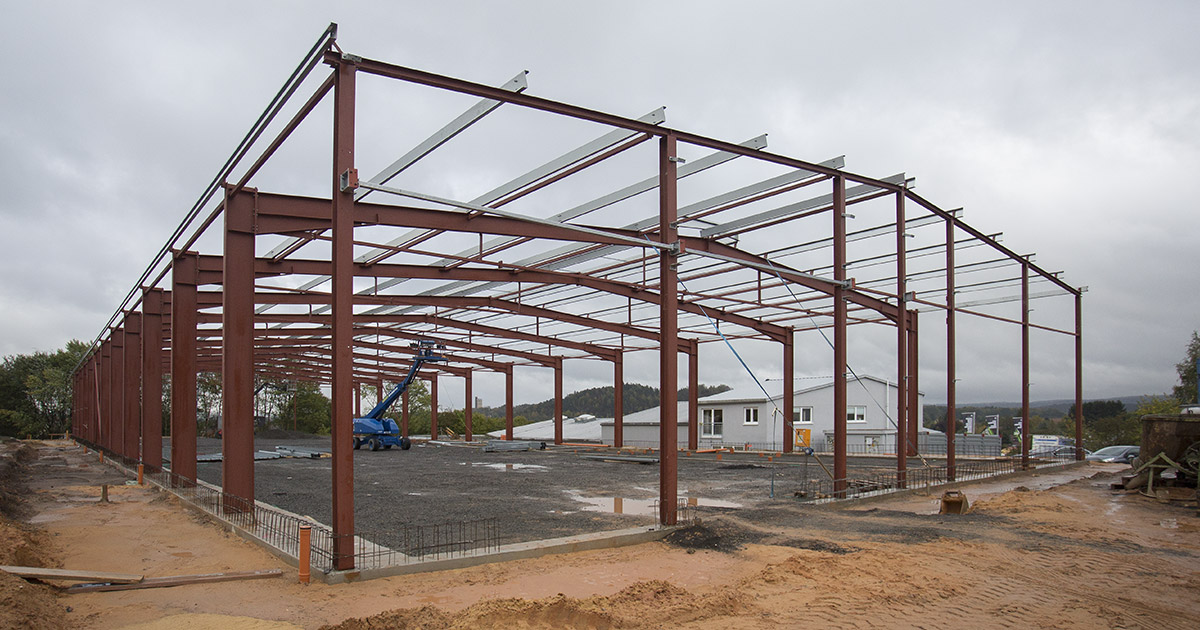
2014
- Details
- Kategorie: Unternehmensgeschichte
Im September beginnen die Bauarbeiten am neuen Versand- und Logistikzentrum. Hierfür wird ein benachbartes Grundstück gekauft, um in einem ersten Schritt eine Halle mit rund 1.800 m² zu errichten.
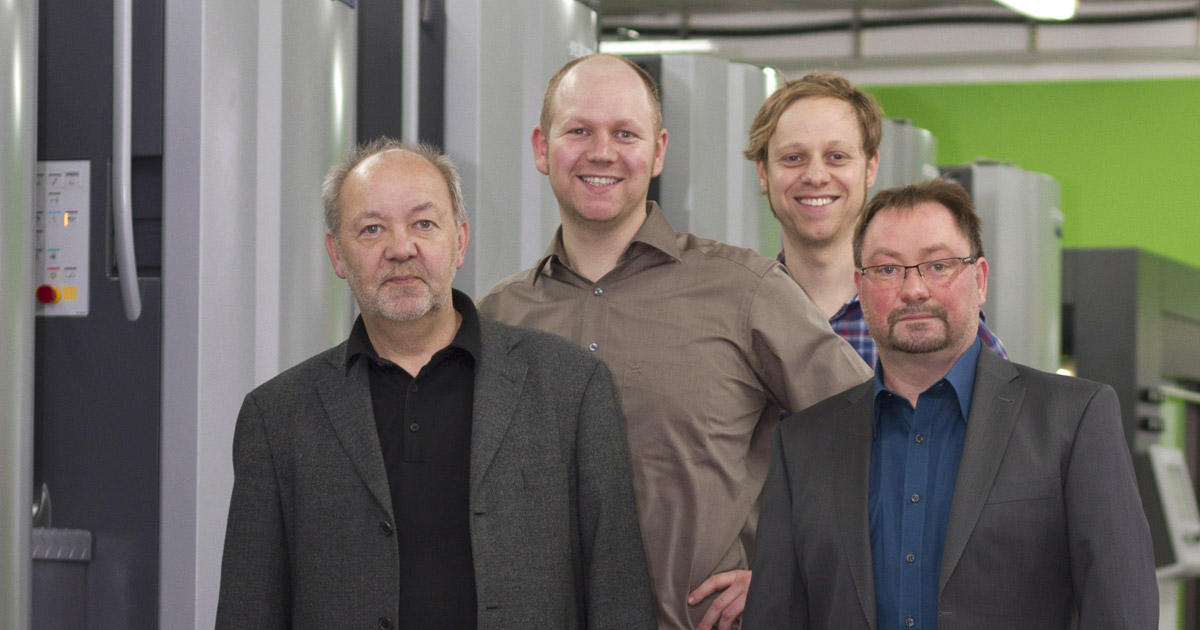
2013
- Details
- Kategorie: Unternehmensgeschichte
Holger Kern tritt neben Jürgen und André Kern in die Geschäftsführung ein. Er tritt die Nachfolge von Joachim Kern an, der zum Jahresende aus der Geschäftsführung in den Ruhestand verabschiedet wird.
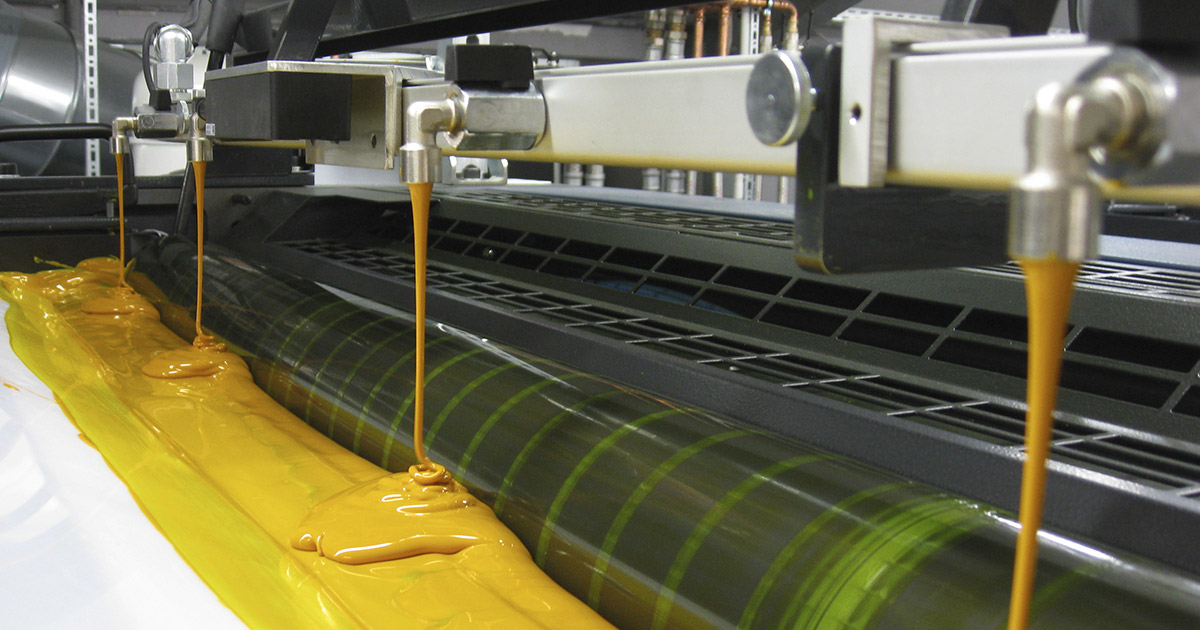
2012
- Details
- Kategorie: Unternehmensgeschichte
Im Februar wird die SM 102 8P im Offsetdruck durch die weltweit erste Heidelberg Speedmaster SX 102 8P ersetzt. Die SX 102 durchläuft bei Kern einen dreimonatigen Feldtestbetrieb, bevor sie im Mai auf der drupa in Düsseldorf offiziell der Weltöffentlichkeit präsentiert wird.
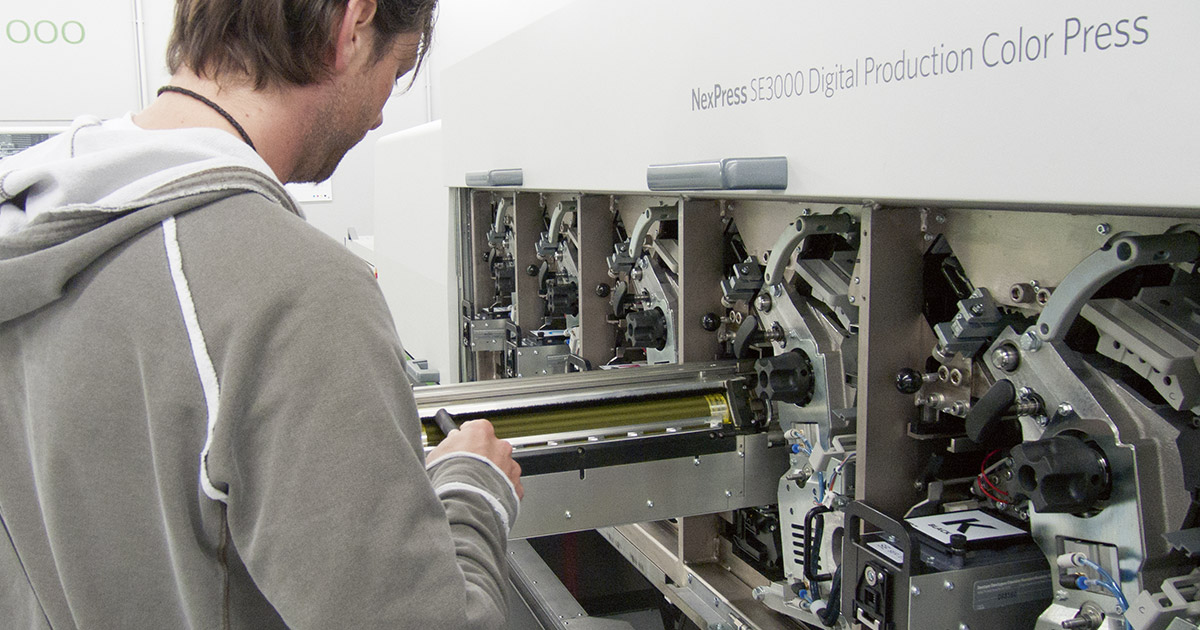
2011
- Details
- Kategorie: Unternehmensgeschichte
André Kerns Bruder Holger Kern tritt ins Unternehmen ein.
Im März erfolgt erstmals die erfolgreiche Zertifizierung nach PSO – Prozessstandard Offsetdruck (ISO 12647). Damit garantiert das Unternehmen eine konsequent gute Farbwiedergabe über die gesamte Offsetproduktionskette, von der Datenerstellung und -bearbeitung über die Druckplattenbelichtung bis zum Druck selbst. Die Einhaltung dieser Norm wird alle zwei Jahre von externen Auditoren geprüft.
2010
- Details
- Kategorie: Unternehmensgeschichte
Kern kann gleich mit drei Weltneuheiten aufwarten. Die erste Heidelberg Speedmaster CX 102 5C Offsetdruckmaschine nimmt, nach einer dreimonatigen Feldtestphase im eigenen Haus, ihren regulären Produktionsbetrieb auf. Für die Mailingproduktion wurde die Eigenentwicklung Heidelberg Perfektor Flexomailer installiert. Mit weltweit einmaliger Bogenwendung im Format 70 × 100 cm und der kompletten Inline-Verarbeitung können so Selfmailer in noch nicht dagewesener Qualität und Geschwindigkeit produziert werden. Die Personalisierung erfolgt beidseitig mit sechs Inkjet-Druckköpfen des Kodak-Prosper-S10-Systems in Laserdruckqualität bei einem Durchsatz von über 300 Metern pro Minute. Die Kern GmbH verfügt damit über das weltweit erste Prosper-S10-System im Bogeneinsatz.
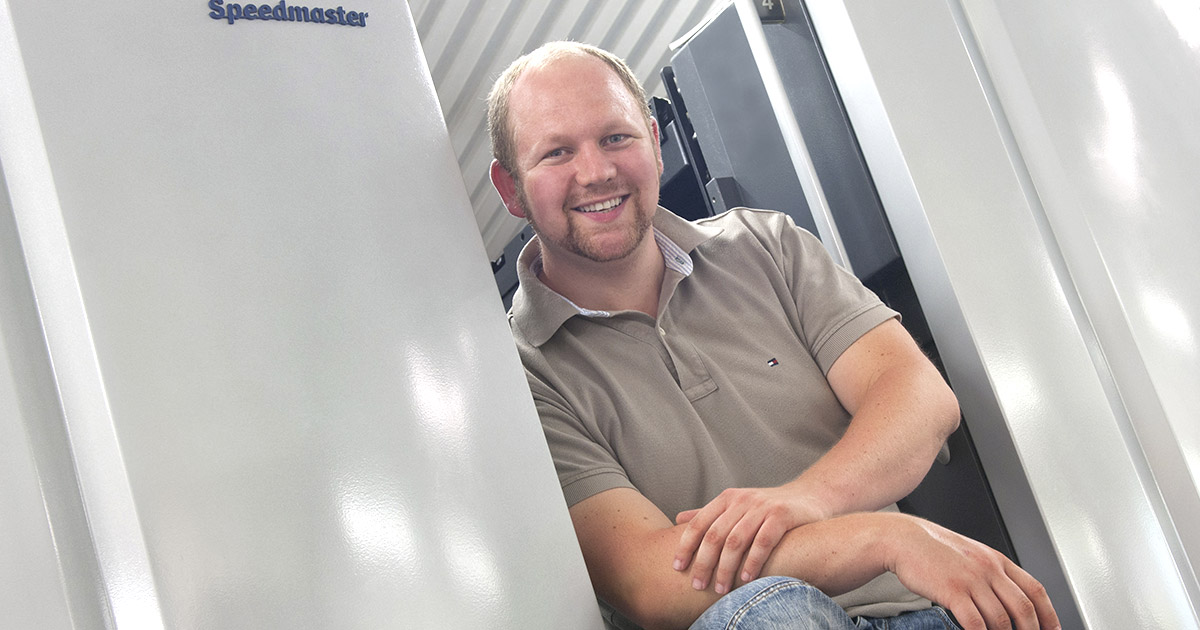
2008
- Details
- Kategorie: Unternehmensgeschichte
André Kern tritt neben seinem Vater Jürgen Kern und dessen Bruder Joachim Kern in die Geschäftsführung ein.
Druckplatten werden nun mit einem Heidelberg Suprasetter 105 SCL Autoloader mit bis zu 19 großen Platten pro Stunde im 24-Stunden Betrieb belichtet. Das neu installierte Heidelberg Image Control System gewährleistet eine konstant hohe Druckqualität, sowohl an der Speedmaster SM 102 6C, als auch an der neuen SM 102 8C.
2007
- Details
- Kategorie: Unternehmensgeschichte
One-Pass-Productivity ist mit der Installation der Heidelberg Speedmaster SM 102 6C auch bei Kern in den Focus gerückt. Seither können mittels Stanzblechen oder Cito-Systemen in einem Druckwerk nun Weiterverarbeitungsschritte wie Stanzen, Perforieren und Rillen direkt beim Druckvorgang vorgenommen werden. Mit der SM 102 6C sind erstmals auch Veredelungseffekte wie Spotlack im großen Format möglich, die bis dahin nur von der kleinformatigen Speedmaster SM 52 5C+LX produziert werden konnten.
2006
- Details
- Kategorie: Unternehmensgeschichte
Um dem wachsenden Qualitätsanspruch der Kunden gerecht werden zu können, werden die ersten sechs Mailings bzw. Selfmailer von der Deutschen Post zertifiziert. Der Lettershop intensiviert die Zusammenarbeit mit der Post, so dass die Kern GmbH seit 2006 offiziell zu den Performance Partnern der Deutschen Post gehört.
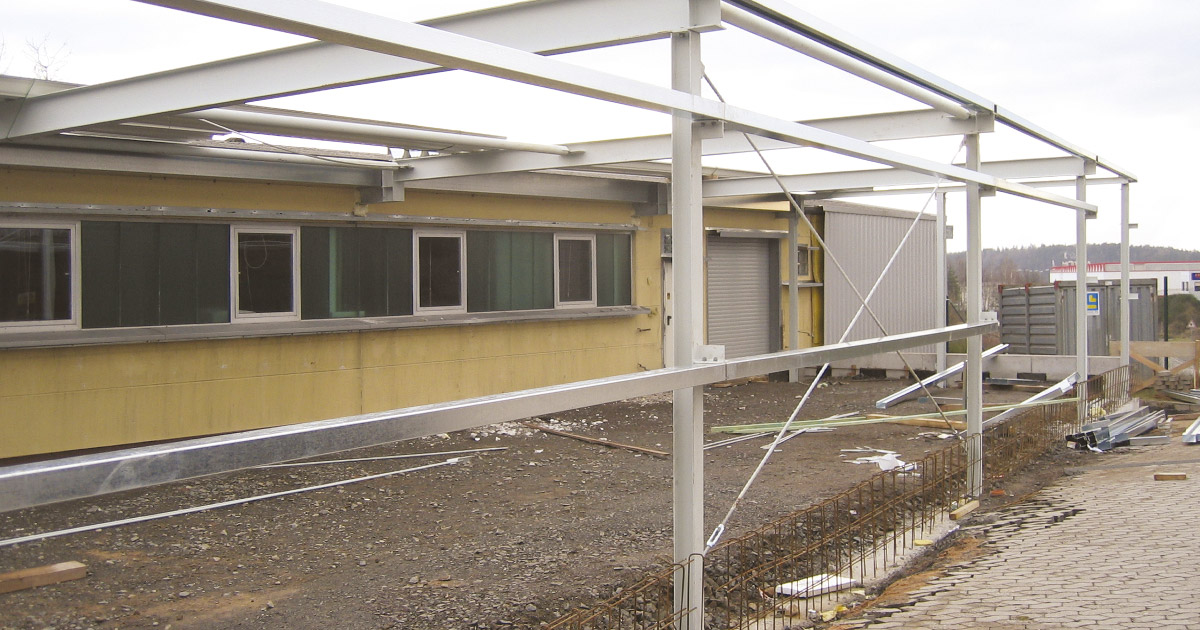
2005
- Details
- Kategorie: Unternehmensgeschichte
Die bisherige Offsetdruckstraße wird durch eine Heidelberg Speedmaster 8C 4/4 ersetzt. Dank automatischer Bogenwendung und drastisch verkürzten Rüstzeiten kann eine Verdoppelung der Kapazität im 4/4-Farbbereich erreicht werden. Zusammen mit dem eigens für die neue Offsetdruckmaschine errichteten Erweiterungsbau werden ca. 3 Millionen Euro investiert und die Gesamtproduktionsfläche auf 1800 m² vergrößert. Die Zahl der Mitarbeitenden steigt auf 28 in Bexbach plus drei weiterer im Tochterunternehmen in Saargemünd.
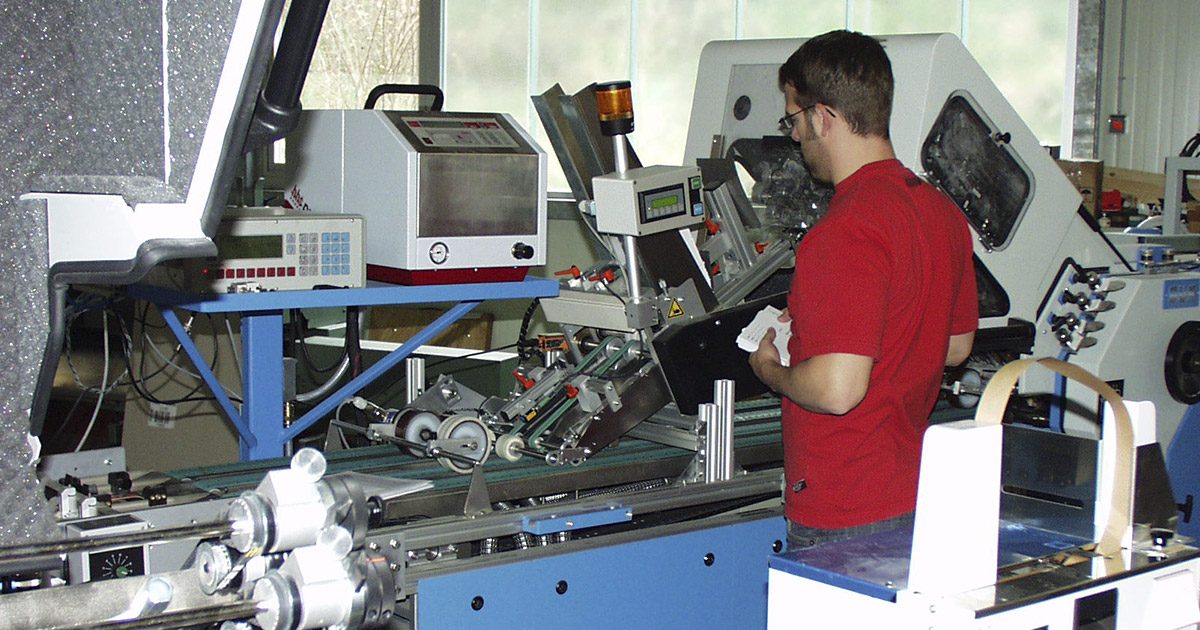
2000er
- Details
- Kategorie: Unternehmensgeschichte
In den Jahren 2003 bis 2005 wird die Mailingproduktion weiter ausgebaut. Mailings werden nun mit mehreren Inkjet-Personalisiereinheiten und zwei Pitney Bowes Post Star Vitesse Kuvertiermaschinen mit vier bzw. sechs Stationen produziert. Eine im Sondermaschinenbau hergestellte Mailinganlage ermöglichte inline Falzen, Personalisieren, Aufspenden von Response-Elementen, Verkleben und Perforieren in einem Arbeitsgang und damit die effiziente Produktion von Selfmailern. Die jährliche Ausbringungsmenge wird so auf über 10 Millionen Mailings gesteigert.
2002
- Details
- Kategorie: Unternehmensgeschichte
Der Offsetdruck wird um eine Heidelberg Speedmaster SM 52 5C+LX ergänzt. Mit der neuen Maschine können Druckveredelungen wie Spotlack erzeugt werden. Zudem können Weiterverarbeitungsschritte wie Inline-Stanzen, Perforieren, Nuten direkt im Druckdurchgang vorgenommen werden.
2001
- Details
- Kategorie: Unternehmensgeschichte
Die Übernahme der Druckerei Litholaser SARL in Saargemünd eröffnet nicht nur einen neuen Markt im angrenzenden Frankreich, sondern mit dem Großformatdruck auch einen weiteren Geschäftszweig, der heute zu einem der Kernbereiche in der Produktion geworden ist.
1999
- Details
- Kategorie: Unternehmensgeschichte
Durch die stetige Erweiterung der Druckerei muss Raum für weitere Kapazitäten geschaffen werden. Im November 1999 erfolgt darum der Umzug ins Gewerbegebiet In der Kolling nach Bexbach in eine ehemalige Kofferfabrik mit einer Produktionsfläche von 1.400 m². Mit dem Umstieg von der Heidelberg MO 4C auf eine neue Heidelberg SM 102 4C 2/2 wird der Formatwechsel auf 72 × 102 cm vollzogen. Daneben sind u.a. noch eine Heidelberg Quickmaster 46 2C und ein GTO 46 1C im Offsetdruck im Einsatz.
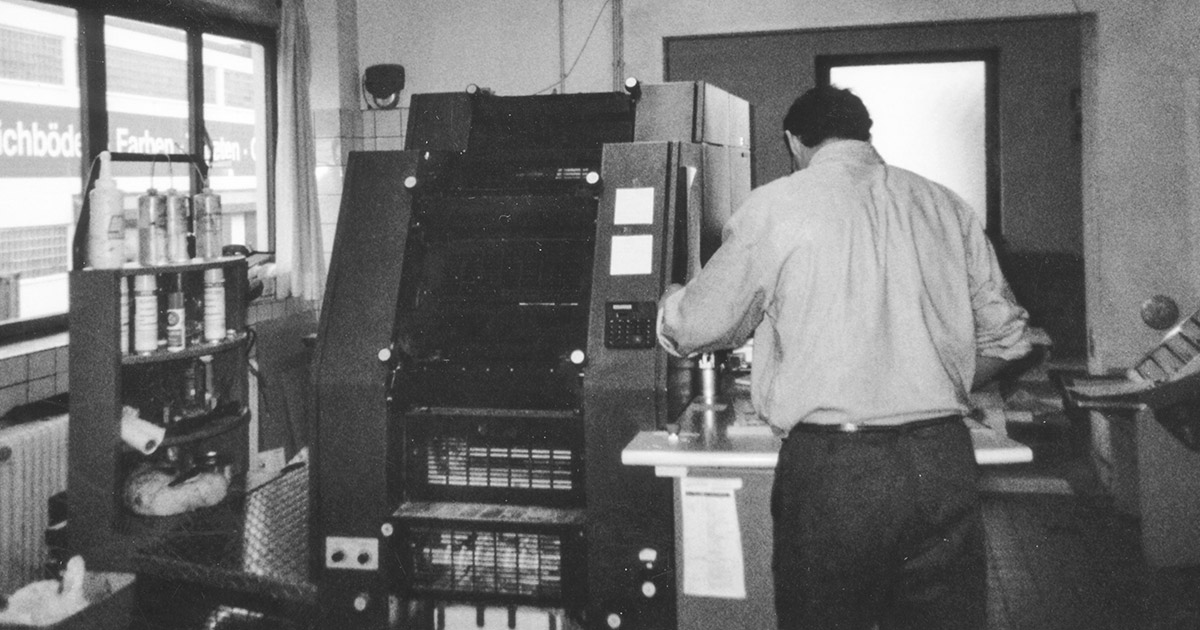
1996
- Details
- Kategorie: Unternehmensgeschichte
Erste Erfahrungen im Digitaldruck werden ab 1996 gesammelt – eine der ersten Heidelberg Quickmaster DI in Deutschland wird bei Kern installiert. Dank des Computer-to-Press-Verfahrens konnten die Druckplatten direkt im Druckwerk bebildert werden. Später folgt eine Agfa Chromapress.
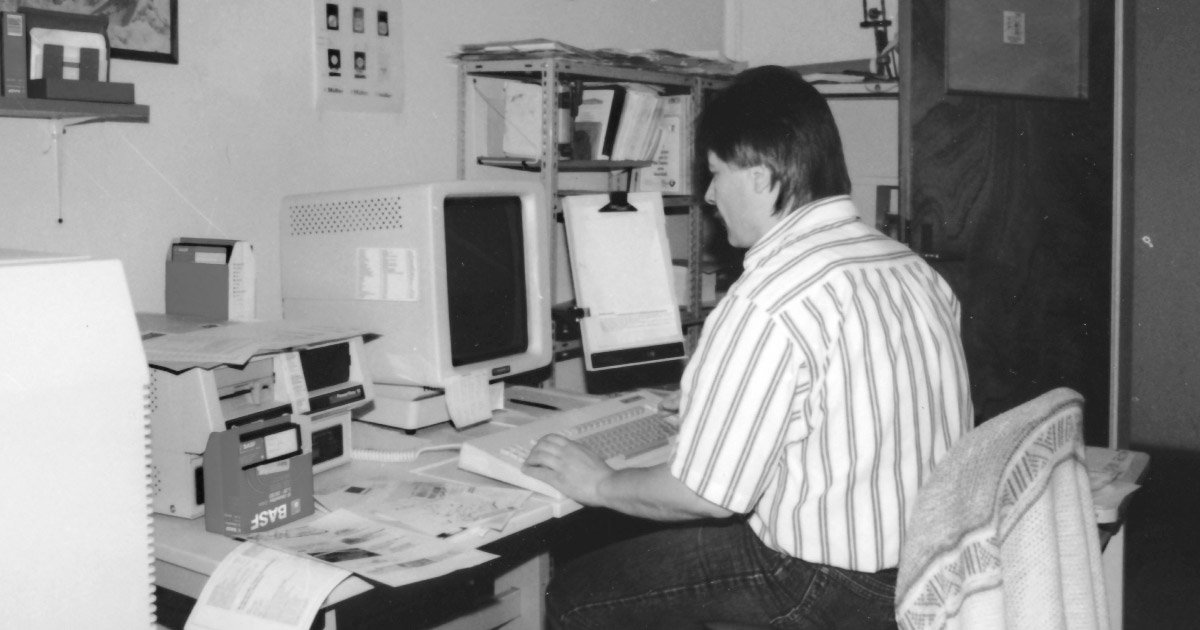
1980er
- Details
- Kategorie: Unternehmensgeschichte
Die Firmierung zur heutigen GmbH erfolgt 1983 mit der Übernahme der Druckerei durch Jürgen Kern, Sohn von Alois Kern. 1985 steigt auch sein Bruder Joachim Kern mit in die Leitung des Unternehmens ein.
Die manuelle Montage von Positiv- und Negativfilmen hat Anfang der 80er Jahre ihr Ende mit der Installation eines Computer-to-Film-Belichters. Mit ihm können ganzseitige Filme belichtet werden, was zu diesem Zeitpunkt im Saarland sonst nur noch der Saarbrücker Zeitung möglich war.
1979
- Details
- Kategorie: Unternehmensgeschichte
Aus dem Schreibwarenladen mit Druckerei im Hinterhof wird ein reiner Druckereibetrieb. Das Unternehmen zieht von der Wellesweiler Str. 12 in die Hausnummer 218.
Erfolgt die Druckplattenherstellung zunächst noch analog mittels Reprofotografie und Handmontage, hält Ende der 70er Jahre die digitale Satzerstellung Einzug ins Unternehmen. Mit dem Fotosatzgerät Compugraphic EditWriter 7500 können erstmals ganze Layouts am Computer erstellt werden.
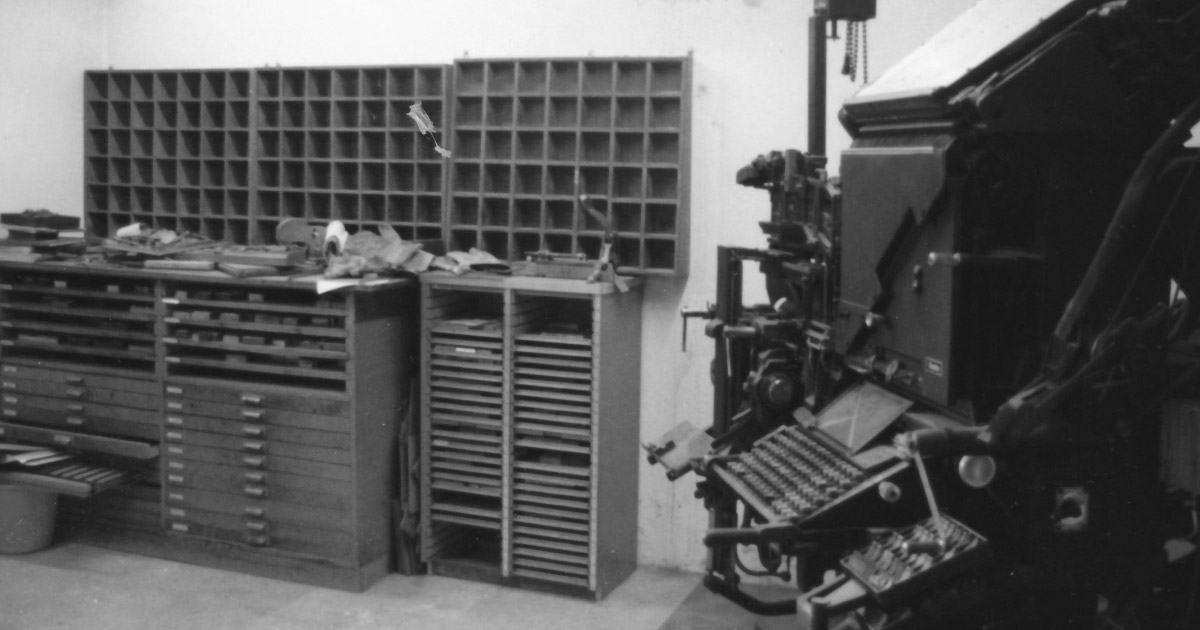
1970er
- Details
- Kategorie: Unternehmensgeschichte
Gedruckt wird ursprünglich im Hochdruckverfahren auf Albert Frankenthal Zylinder und Original Heidelberger Tiegel (OHT) – zunächst noch im Handsatz, später mit Linotype maschinell gesetzt.
Mitte der 1970er Jahre erfolgt der erste Technologiesprung beim Umstieg auf Offsetdruck mit einer Kord Druckmaschine im DIN A2 Format und einer einfarbigen Heidelberg GTO 46 (Format A3+).
Es folgen eine zweifarbige Edelmann Praktika, sowie zwei Heidelberg MO 2C, die den Weg zum Vierfarbdruck in einem Durchgang bereiten, der schließlich mit dem Wechsel auf eine Heidelberg MO 4C im Format 46 × 65 cm vollzogen wird.
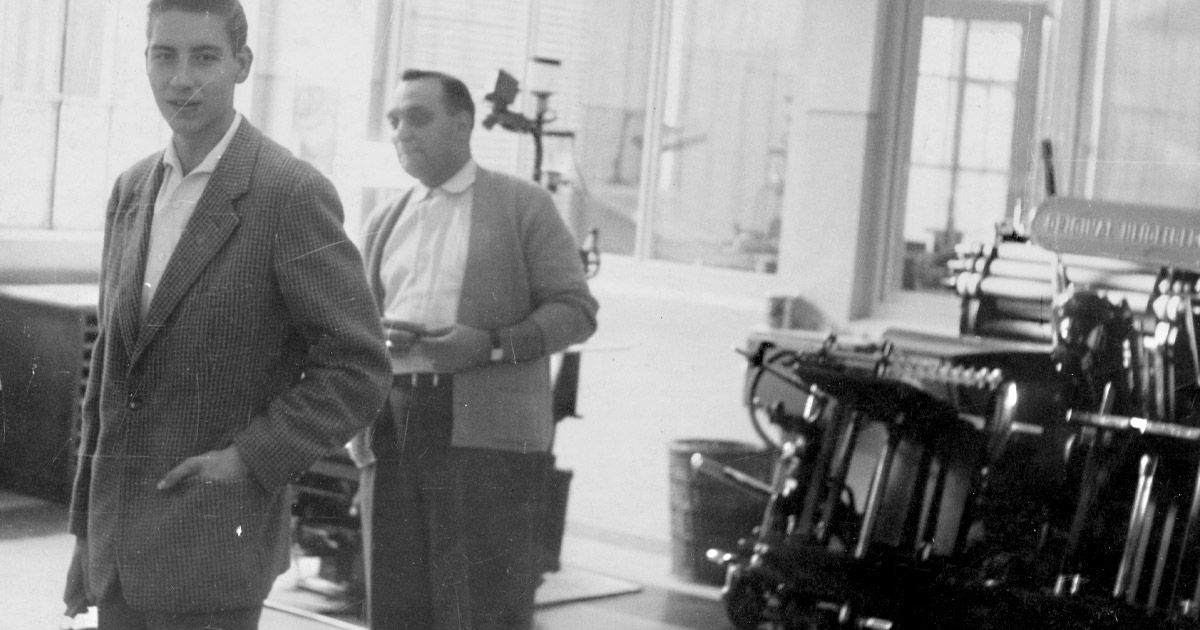
aus Beine wird Kern
- Details
- Kategorie: Unternehmensgeschichte
Der Namenswechsel erfolgt mit der Hochzeit von Alfred Beines Tochter Hilde und Alois Kern, der die Familientradition in Neunkirchen festigt und erfolgreich fortführt.
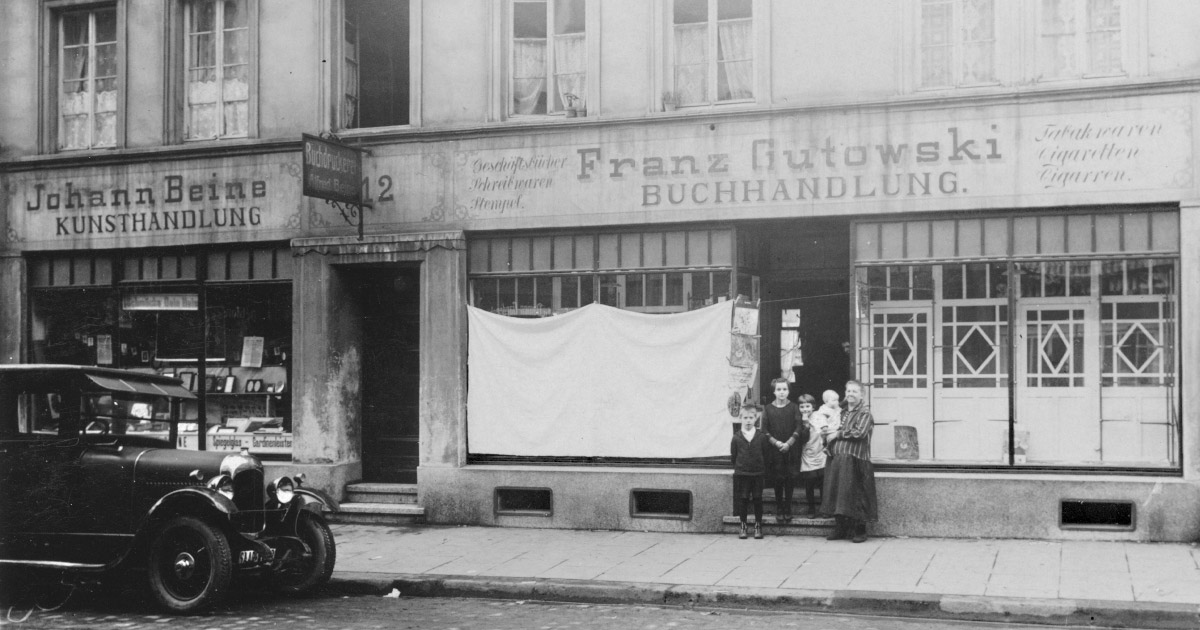
1911
- Details
- Kategorie: Unternehmensgeschichte
Alfred Beine führt das Geschäft seines Vaters fort und erweitert es um eine Rahmenwerkstatt. Die Familie übernimmt später die benachbarte Buchhandlung mit Schreibwarengeschäft.
1897
- Details
- Kategorie: Unternehmensgeschichte
Johann Beine übernimmt das Geschäft von seinem Vater und erweitert es um eine Buchdruckerei.
1862
- Details
- Kategorie: Unternehmensgeschichte
Den Grundstein der heutigen Druckerei Kern mit Sitz im saarländischen Bexbach legte Ludwig Beine in der zweiten Hälfte des 19. Jahrhunderts. Die Wurzeln der Familie Beine liegen in Warburg, Nordrhein-Westfalen. 1862 zog Ludwig Beine in die Hüttenstadt Neunkirchen und gründete in der Wellesweiler Str. 12 Buchhandlung mit angeschlossener Handbuchbinderei.